Reverse FMEA: A Practical Approach to Reinforce Manufacturing Process Robustness
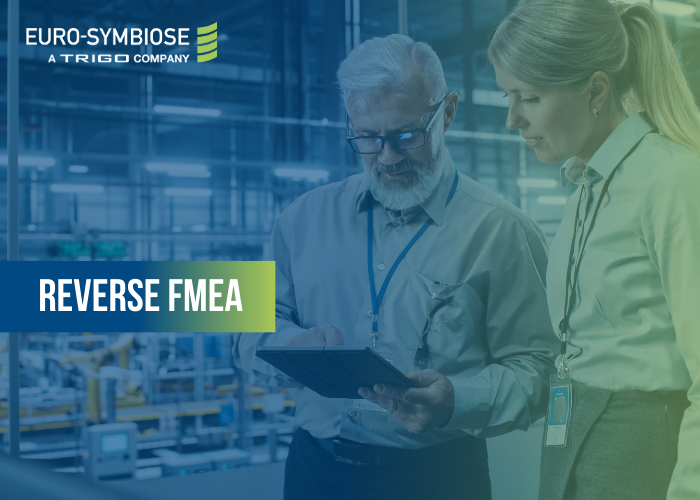
More and more automotive OEMs, such as STELLANTIS, RENAULT, FORD, GM, and Tier 1 suppliers, are requiring the implementation of Reverse FMEA during series production. But what exactly is this method, and what tangible benefits can it bring to your company?
Reverse FMEA is a shop-floor-based approach that complements traditional risk analysis tools—primarily the Process FMEA, and potentially the Control Plan or Machinery FMEA. This pragmatic method focuses on verifying the effectiveness of existing controls in manufacturing processes and product quality, by confronting the real-world execution with the theoretical analysis of Failure Modes, their Effects, and Criticality.
It is a continuous improvement tool that assesses the robustness of running production processes, while also integrating real-life feedback in order to update both generic and specific Process FMEAs for current and future installations.
The Main Objectives of Reverse PFMEA
Reverse PFMEA is used to verify whether all prevention and detection actions, defined during the initial project-phase Process FMEA, have been properly implemented, are effective, and remain relevant in actual production. It also ensures that the assumptions made during the original risk analysis were accurate and genuinely help reduce the identified risks.
Moreover, this method may reveal new failure modes that were not initially identified. It should be noted that the initial Process FMEA aims to be as exhaustive as possible regarding the highest-risk points, but it is sometimes difficult to consider all potential failure sources and their causes due to a lack of return of experience or limited resources.
The ultimate goal is to make the PFMEA a living document—updated and enriched with on-the-ground observations—adding real value to the methodology. It allows companies to reconnect with the FMEA approach by fostering a continuous improvement dynamic, leading to better risk management and measurable results such as reduced internal scrap rates and fewer customer complaints.
How Reverse PFMEA is Carried Out
Reverse PFMEA takes place directly on the shop floor, in the front of the machines and installations. This walkthrough focuses on critical points and is carried out by a multidisciplinary team (production, industrialization, maintenance, quality, etc.), so that all departments involved can share insights on the effectiveness of controls defined during process development or in a previous Reverse PFMEA session.
The Preparation Phase
This first phase consists of identifying priorities for the shop-floor analysis. This involves collecting process-specific input data (product specifications, safety/regulatory/critical features, process flow charts, control plans, production quality indicators, customer complaints, etc.), and selecting specific PFMEA lines to review based on criteria such as severity index, RPN, or AP ratings.
The Shop-Floor Analysis Phase
The second phase is the core of the Reverse FMEA: observing how well the planned controls are being applied in practice. The team interacts with operators, supervisors, quality and maintenance technicians—those who are closest to existing process issues, which may not always be escalated or properly addressed.
This is also the time to observe production, handling, and storage operations, and to identify potential failure modes that were missed during the initial PFMEA.
In some cases, new failure modes can be simulated—such as missing parts, misaligned components, or incorrect material dosage—to see whether the process is capable of preventing defects or detecting them immediately or downstream. These simulations must be carried out with care to avoid damaging equipment or contaminating production flow with wrong parts.
At the end of this phase, if new risks are identified, immediate containment actions may be necessary to protect the customer while corrective measures are put in place.
Reverse FMEA Output
The third and final phase involves updating the original Process FMEA with the new findings—adding newly identified failure modes and their root causes, and revising occurrence and detection ratings based on real-world performance data. This may also trigger new risk control actions and updates to associated documentation, such as control plans, work instructions, and maintenance plans.
As outlined, Reverse FMEA is a pragmatic and concrete methodology that aligns risk identification, corrective actions, and documentation with the realities of production.
Planning Reverse FMEA Activities
Customers are asking suppliers to schedule Reverse FMEA activities. This planning should remains flexible and triggered by specific events such as the launch of a new production line, product or process changes, customer complaints, or high scrap rates.
There is no mandatory frequency imposed, but the implicit expectation is to make it a dynamic tool for revising the Process FMEA. It is therefore recommended to hold shorter but more frequent sessions (e.g., 2 to 3 hours per month) rather than relying on an annual review, as is often the case with other quality tools.
Want to Learn More and Practice the Method?
TRIGO offers two dedicated training modules:
- Reverse FMEA – The Method (1 Day): Delivered onsite or remotely, this course introduces the methodology using a standard case study.
- Reverse FMEA – Full Deployment (2 Days): Onsite application of the complete methodology in your own context, directly on your shop floor, leading to a real update of your FMEAs.
With these sessions, you’ll be able to demonstrate to your customers that you have mastered the methodology and are using it as a tool for continuous improvement.
Go Further
Explore the following TRIGO training programs dedicated to Reverse FMEA:
- Reverse FMEA – The Method (1 day)
- Reverse FMEA – Full Deployment (2 days)