Production workstations audit : a process for optimizing performance and safety
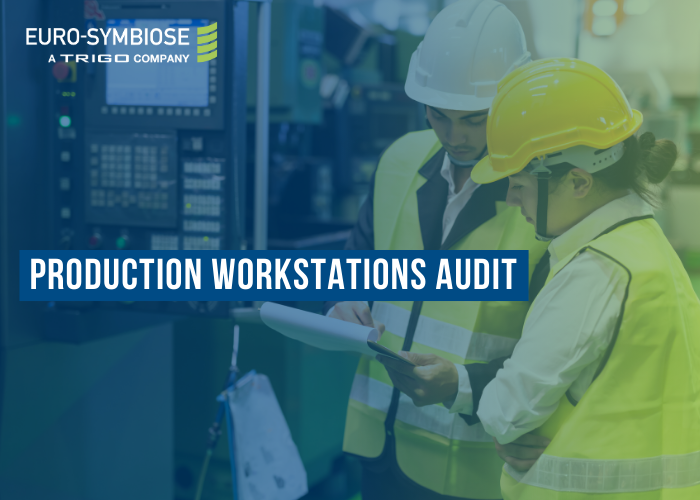
The value and usefulness of workstation audits
Workstation audits are an essential part of industrial processes, complementing system, process, and product audits. The process involves evaluating and improving the performance of different workstations within a factory. In an environment where quality, safety, and efficiency are paramount, workstation audits help identify strengths and weaknesses in operational processes.
The objectives of workstation audits
One of the main objectives of a workstation audit is to ensure compliance with quality and safety standards, as well as the company’s own performance standards. This includes assessing the proper application of work procedures, the use of equipment, and the appropriate qualifications of employees in their positions.
Another key objective is to optimize the efficiency of the production process. Job audits make it possible to analyze workflows, identify bottlenecks, and suggest improvements. This can lead to reduced downtime, better use of both human and material resources, increased overall productivity, and better consideration of risks, ergonomics, and movement in the workplace.
Workstation audits also enable results to be compared by manufacturing sector (cutting, injection, heat treatment, assembly, etc.), which helps identify the stages of the process where there are more risks.
By identifying deviations from standards and areas for improvement, organizations can implement corrective and preventive actions. This helps to guarantee and improve quality, cost, and delivery performance, compliance with applicable regulations, safety, and also the motivation of production personnel.
Implementation of the workstation audit
The workstation audit comprises several steps:
- Create checklists including the standards to be verified at the workstation and the evaluation criteria.
- Define who will be in charge of workstation audits, depending on each organization, most often quality technicians, team leaders, or team managers.
- Plan audits, prioritizing them through a risk analysis based on previous audit history, internal incidents, customer complaints, and the results of system, product, and process audits, as well as considering available resources.
- Conduct audits through workplace observations, discussions with staff, and analysis of workplace instructions. This information is then analyzed to identify trends and areas for improvement.
- Alert and resolve discrepancies by implementing corrective actions immediately to comply with workplace standards.
- Write the report using the checklist to be completed with discrepancies, areas for improvement, and associated actions.
- Implement actions according to the responsibilities defined and committed to within the organization.
- Conduct an annual review of the audit results as part of the management review input to assess the effectiveness of the audit program (ISO 9001:9.3.2).
In conclusion, job audits help create a safer and more efficient work environment by promoting a proactive approach to process management. In addition, it helps to increase customer satisfaction by ensuring that products are delivered on time and in accordance with specifications. Job audits are an essential tool for companies wishing to remain competitive in a constantly changing market. By investing time in regular audits and the resulting actions, companies can improve their operational performance.
To go further
Euro-Symbiose offers training dedicated to the implementation of effective job audits. This training is intended for quality, maintenance, and logistics personnel. Euro-Symbiose can also assist you in implementing your job audits.